При сборке подшипниковых узлов должны выполняться следующие технические условия:
1. Кольца и тела качения подшипника должны быть чистыми, без заметных дефектов. При вращении от руки подшипник должен вращаться свободно, без значительного шума. Новый подшипник с неповрежденной упаковкой и незагустевшей смазкой можно не промывать. Загрязненные подшипники промывают в бензине с добавлением 6-8 % минерального масла или в масле (Индустриальное 12 или 20) в ванне с электроподогревом при температуре 60-90 °С в течение 15-20 мин. Сильно загрязненные подшипники промывают дважды. После промывки подшипник просушивают на бумаге или с помощью сжатого воздуха. Пятна коррозии на подшипнике удаляют мягкой шкуркой и пастой ГОИ с последующей промывкой.
2. Осевой и радиальный зазоры в подшипнике должны быть в допускаемых пределах. Схема замера зазоров приведена на схеме. Величина начальных зазоров для подшипников различных типов приведена в специальной литературе.
3. Посадочные места в корпусе и на валу должны быть точно и чисто обработаны. Перед сборкой подшипникового узла посадочные места промывают керосином, просушивают и смазывают. Механические повреждения, забоины, вмятины, следы коррозии устраняют. Диаметры шеек валов контролируют с помощью предельных скоб и микрометров, а диаметры отверстий корпусов - предельными пробками, индикаторными нутромерами или штихмассами.
4. Во избежание перекоса радиус закругления галтели на валу (при отсутствии кольцевой проточки или выточки) должен быть меньше, чем радиус фаски у подшипника. Величину радиуса галтели проверяют с помощью радиусомера или шаблона.
5. Упорный заплечик вала или отверстия в корпусе должен быть перпендикулярен к посадочным поверхностям. Допускаемое торцовое биение приведено в таблице. Перпендикулярность заплечиков вала и корпуса оси посадочного места проверяют угольником или индикатором.
6. Недопустимо попадание в подшипниковый узел грязи или абразива, что приводит к ускоренному изнашиванию подшипника.
7. При правильной сборке подшипник должен работать плавно и бесшумно, а также не нагреваться выше 70 °С.
8. Выбор посадки подшипника на вал и в отверстие корпуса зависит от типа машины, требований к точности вращения, характера нагрузки, типа, размера и условия монтажа подшипника. Необходимая посадка подшипника обеспечивается за счет допусков на диаметры вала и отверстия корпуса. На сборочных чертежах и чертежах деталей рядом с номинальным размером дается условное обозначение поля допуска только поверхности, сопряженной с подшипником.
9. Для обеспечения правильной установки подшипника на вал и в корпус следует применять специальные приспособления. При запрессовке подшипника на вал или в корпус используют монтажные трубы из мягкого металла, винтовые и гидравлические прессы. Усилие запрессовки прикладывается к тому кольцу подшипника, которое устанавливается с натягом, а при запрессовке одновременно на вал и в корпус - к обоим кольцам. Для облегчения работы вал может охлаждаться, а корпус нагреваться, подшипник, соответственно, либо нагреваться, либо охлаждаться.
10. После сборки проверяют по периметру прилегание подшипника к заплечику вала и корпуса, вхождение щупа 0,03 мм и более не допускается.
11. Отсутствие перекоса подшипника при установке его вместе с валом в корпус проверяют свободным проворотом вала вручную.
12. Во избежание защемления тел качения подшипники, устанавливаемые с предварительным натягом, должны иметь плавный ход и незначительный шум при провороте от руки, а в подшипниках без предварительного натяга, кроме того, должен ощущаться небольшой осевой люфт.
Cтраница 1
Сборка подшипников качения является редкой операцией при монтаже оборудования химических заводов. Обычно машины и аппараты поступают для монтажа с подшипниками, установленными на заводе-изготовителе.
Посадка подшипников качения. |
Сборка подшипников качения осуществляется с натягом на вал, в корпус или на вал и в корпус.
Индукционно-тешю-ван сборка подшипников качения с валами.
При сборке подшипников качения возможны следующие дефекты. Овальность внутреннего кольца радиального подшипника появляется вследствие неправильной напрессовки на вал. Перекос колец при сборке ведет к выкрашиванию их краев. Проворачивание колец на валу или в корпусе приводит к нагреву подшипника и появлению вибраций. При сборке нужно следить за тем, чтобы неподвижное кольцо имело возможность самоустанавливаться для компенсации температурных удлинений. При запрессовке подшипников качения часто необходим нагрев их в масляной ванне до 80 - 100 С.
Образование натяга в ралиально-упорных подшипниках при их монтаже.| Схема приспособления для проверки радиального зазора в шарикоподшипнике после его нанрессовки на вал. |
При сборке подшипников качения особое внимание следует обращать на чистоту рабочего места, сборочных приспособлений и сопрягаемых деталей.
При сборке подшипников качения нельзя ударять молотком непосредственно по кольцам или сепаратору; это может привести к перекосу колец, поломке или повреждению сепаратора. Нельзя также Применять свинцовые и баббитовые молотки, так как от них могут отскакивать кусочки металла и попадать между телами качения подшипника.
При сборке подшипников качения возможны следующие дефекты. Овальность внутреннего кольца радиального подшипника появляется вследствие неправильной напрессовки на вал. Перекос колец при сборке ведет к выкрашиванию их краев. Проворачивание колец на валу или в корпусе приводит к нагреву подшипника, появлению вибраций. При сборке необходимо следить за тем, чтобы неподвиж - - MQJLJJOgbso имело возможность самоустанавливаться для компенса-ции температурных удлинений.
При сборке подшипников качения с деталями обычно вращающееся кольцо подшипника, сопряженное с валом, имеет посадку с натягом и вращаться на валу не должен. Неподвижное кольцо-подшипника в корпусе может иметь более слабую посадку, при которой он может незначительно провертываться. Посадка подшипников качения на вал осуществляется по системе отверстия, посадка в корпусе - по системе вала.
При сборке подшипников качения следует соблюдать технические, условия, которые устанавливаются ГОСТами, отраслевыми нормалями ВНИППа и заводскими ТУ.
При сборке подшипников качения с деталями обычно вращающееся кольцо подшипника, сопряженное с валом, имеет посадку с натягом и вращаться на валу не должен. Неподвижное кольцо подшипника в корпусе может иметь более слабую посадку, при которой он может незначительно провертываться. Посадка подшипников качения на вал осуществляется по системе отверстия, посадка в корпусе - по системе вала. Таким образом, при сборке подшипников, при установке внутреннего кольца на вал и наружного кольца в корпус детали применяют в обоих случаях неподвижные посадки, но характер посадок различен.
Следующая страница>>Сборка узлов с подшипниками качения. Напрессовка подшипников.
Сборка узлов с подшипниками качения выполняется следующим образом. При монтаже подшипников необходимо создать зазоры, обеспечивающие свободное, без защемления шариков или роликов вращение подшипников. При слишком плотной посадке происходит расширение внутреннего кольца подшипника и сжатие его наружного кольца, в результате чего шарики или ролики защемляются и подшипник быстро выходит из строя. Чрезмерный зазор в посадочных местах также ухудшает работу подшипника: кольца его начинают проскальзывать, вызывая износ посадочных поверхностей и вибрацию механизма.
Перед сборкой подшипники тщательно промывают в смеси бензина и минерального масла или в обезвоженном чистом керосине. Промытые подшипники укладывают на чистую бумагу и просушивают или обдувают сжатым воздухом. Сразу после просушки их смазывают, покрывая тонким слоем масла все поверхности, особенно внутренние дорожки качения, шарики и ролики. Посадку подшипников на вал производят по системе отверстия, а в корпус- по системе вала.
Посадка подшипников на залы, в гнезда корпусов деталей может быть выполнена при помощи ручных, гидравлических или пневматических прессов; с подогревом в горячем масле (80-90° С) или с охлаждением твердой углекислотой - сухим льдом (температура - минус 75-80° С).
Для напрессовки подшипника на шейку вала могут быть использованы ручные приспособления - монтажные стаканы и оправки (рис. 98).
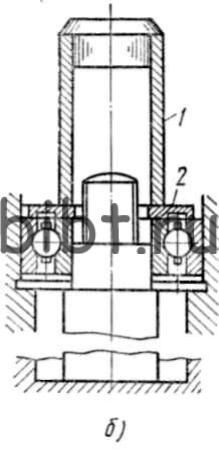
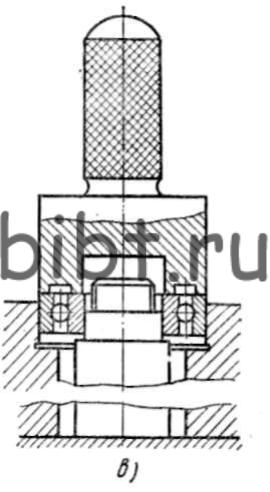
Рис. 98. Оправка для напрессовки подшипников :
а - напрессовка подшипника с помощью оправки и ручного пресса, б- с помощью стакана 1 и кольца 2, в - с помощью ручной оправки
Применение оправок обеспечивает равномерную посадку подшипника на шейку вала, предотвращает перекос при установке и предохраняет подшипник от повреждений. Для напрессовок подшипников на валы, имеющие на конце резьбу, часто используют винтовые устройства (рис. 99, а, б).
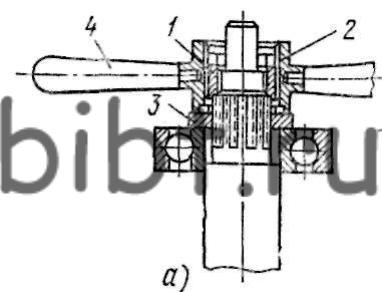
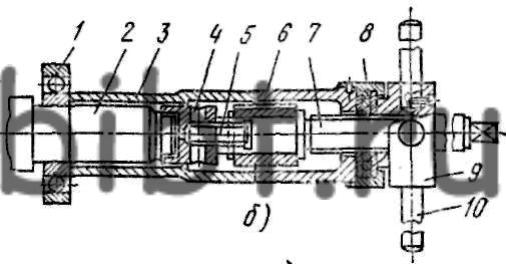
Рис. 99. Приспособления для напрессовки подшипников :
а - гаечное: 1 - гайка, 2 - корпус, 8 - шайба, 4 - ручка; б- винтовое: 1 - подшипник, 2 -вал, 3 - втулка, 4 - гайка, 5 - соединительный винт, 6 - переходная втулка, 7 - винт, 8 - шайба, 9 - корпус, 10 - ручка; в - гидравлическая гайка с насосом
Для напрессовки и распрессовки крупных подшипников применяют гидравлическую гайку (рис. 99, в), которая состоит из корпуса 1 и поршня 2. Поршень имеет две канавки для уплотнительных колец и перемещается в корпусе гайки под давлением масла, подаваемого ручным насосом 4 по трубке 3. Корпус гайки внутри имеет метрическую или трапецеидальную резьбу.
При монтаже подшипников качения следует учитывать, что усилие запрессовки должно передаваться непосредственно на торец сопрягаемого кольца.
В упорных шарикоподшипниках кольца имеют разные диаметры - как наружные, так и внутренние. Чтобы подшипник работал нормально, при сборке следует всегда устанавливать кольцо с меньшим внутренним диаметром на валу, а кольцо с большим внутренним диаметром - в корпусе.
При установке вала в двух радиальных шарикоподшипниках один из них закрепляют неподвижно на валу и в корпусе, а второй - только на валу, потому что вал во время работы нагревается и его длина несколько возрастает. При удлинении вала подшипник перемещается в корпусе. Если закрепить оба подшипника неподвижно, вал, нагревшись, начнет туго поворачиваться и произойдет защемление шариков или роликов и оба подшипника могут быстро выйти из строя. Запрессованный подшипник проверяют, поворачивая его вручную. Вращение подшипника должно быть плавным, без заеданий. При этом может прослушиваться незначительный равномерный шум. Проверяют также прилегание наружного кольца к бортику отверстия корпуса, а внутреннего кольца - к заплечику вала.
Основными дефектами валов и подшипников являются: износ вкладышей и шеек валов, при котором изменяются их диаметр и форма, вследствие чего увеличиваются зазоры между подшипником и валом: изгиб вала, износ шпоночной канавки; царапины, риски и задиры; изгиб вала; износ шпоночной канавки; трещины и расслаивание, а также выплавка баббита в корпусе вкладыша; смятие резьбы и центровых отверстий.
Допустимые параметры износа валов приведены в табл.
Небольшие овальность (до 0,2 мм) и конусность, а также неглубокие задиры, риски и царапины на шейках валов устраняют путем опиливания бархатным напильником и шлифования наждачной шкуркой или притиркой пастой ГОИ с помощью хомута. При более значительных отклонениях и дефектах шейки вала протачивают и шлифуют на станке; однако при этом диаметр шеек не должен уменьшаться более чем на 5%, если вал испытывает ударную нагрузку, и на 10% - при спокойной статической нагрузке.
Шейки вала, имеющие незначительный износ, восстанавливают металлизацией. Шейки вала, работающего при статической нагрузке, при значительном износе восстанавливают электронаплавкой с последующим отжигом и проточкой до номинального диаметра. Шейки наваривают вдоль оси вала, причем каждый навариваемый шов располагают на диаметрально противоположной стороне, так как непрерывная наварка приведет к изгибу вала.
Параметры предельного изгиба валов
Валы и оси с изгибом в пределах, указанных в табл, при отсутствии трещин правят в холодном или горячем состоянии. Правку выполняют с использованием токарного станка и домкрата или специального винтового устройства. В первом случае вал зажимают в центрах станка, под изогнутую часть вала устанавливают домкрат, регулируемый по высоте. Затем с помощью оправки, ударяя по ней молотком, устраняют изгиб вала. При использовании правильной скобы валы небольших диаметров правят в холодном состоянии, а больших диаметров - в горячем. Для этого ват укладывают изогнутой частью вверх и в месте наибольшего изгиба нагревают пламенем газовой горелки или паяльной лампы до 500…600 °С (темно-красное каление). Вращая рукоятку, вал выправляют. Место каления покрывают асбестом и вал медленно охлаждают.
В условиях ремонтно-механических мастерских молочных заводов по рабочим чертежам заводов-изготовителей или по натуральным образцам вытачивают новые неответственные валы для цепных транспортеров, консольных насосов, горизонтальные валы сепараторов и др.
Восстановленный или вновь изготовленный вал проверяют с помощью микрометра и индикатора часовою типа. Вал должен полностью соответствовать рабочему чертежу. Биение вала не должно превышать 0,02-0,06 мм на 1000 мм. На шейках вала не допускается наличие рисок и раковин. В зависимости от материала подшипника твердость поверхности шеек должна быть в пределах НRС 45-56.
Особо ответственные валы, например веретено сепаратора, вал диска распылительной сушилки, восстанавливать и изготовлять на месте запрещается. В случае износа их заменяют новыми.
Небольшие повреждения шпоночных канавок (до 5 % ширины) устраняют опиливанием и шабрением, при значительных повреждениях увеличивают ширину канавки и шпонки (не более 15 % от первоначальной). При большом износе шпонок новую канавку фрезеруют на новом месте под углом 120° (2,094 рад), старую заваривают и зачищают заставленное место.
Нагруженные грани шпонок и шпоночных канавок должны быть тщательно и точно пригнаны одна к другой с опиливанием и шабрением по краске. У врезных шпонок пригоняют по краске боковые поверхности, у тангенциальных – верхнюю и нижнюю поверхности. При этом шпонки не должны упираться в ступицу.
В процессе ремонта подшипников скольжения износ поверхностей трения определяют, измеряя радиальный износ.
В неразъемных подшипниках изношенную втулку заменяют. При запрессовке втулки ее внутренний диаметр уменьшается, поэтому втулку развертывают или подвергают шабрению. Для предотвращения проворачивания втулки в корпусе подшипника при работе сопряжения с большими нагрузками втулку стопорят винтом или штифтом.
У разъемных подшипников для измерения зазора подшипник разбирают, между шейкой вала и вкладышем в крышке помещают два отрезка свинцовой проволоки диаметром 0,5-1 мм. Затем, завинчивая гайки на шпильках крепления крышки подшипника к корпусу, отрезки проволоки сдавливают, после чего соединение разбирают. Измерив микрометром толщину расплющенных проволок, определяют размер зазора. Нормальный зазор в среднем составляет 0,001d, предельно допустимый - 0,004d, где d – диаметр шейки вала. При большем износе подшипник подлежит ремонту. У неразъемных (глухих) подшипников этот зазор является разностью между фактическими размерами диаметра отверстия втулки и шейки вала. В разъемных подшипниках при износе вкладышей их перезаливают или заменяют новыми с последующей механической обработкой и подгонкой по валу с припуском 0,5-1 мм на расточку и 0,05 мм на шабрение. При незначительном (менее 0,004d) износе вкладышей зазор в разъемных подшипниках регулируют «перетяжкой», т. е. удаляют тонкие (толщиной 0,05-1 мм) пластинки, устанавливаемые между корпусом и крышкой подшипника.
После расточки выполняют шабрение вкладышей. Для определения мест шабрения шейки вала окрашивают, укладывают вал на нижние вкладыши корпусов подшипников, накладывают крышки с верхними вкладышами и стягивают крышки с корпусами. Вал проворачивают несколько раз, затем подшипники разбирают и пришабривают каждый вкладыш в отдельности, начиная с нижних. Хорошо пришабренными подшипниками считаются те, которые при проверке равномерно окрашиваются по всей окружности на 70-75% её поверхности. Величину полученного после шабрения зазора можно определить по толщине сплюснутых свинцовых проволок, как было описано выше.
Масляные канавки обрабатывают на фрезерных станках или прорубают крейцмейселем. Для лучшей смазки пары трения края смазочных канавок на поверхности вкладышей сглаживают и округляют.
Местные повреждения рабочих поверхностей втулок или вкладышей (задиры, пленки, раковины, выкрашивания, трещины и частичные отслоения баббитовой заливки площадью до 5% рабочей поверхности) устраняют шабрением. Раковины и выкрашивания больших размеров заплавляют антифрикционным сплавом того же состава, из которого изготовлен вкладыш, а у чугунных втулок – баббитом или бронзой.
При сборке разъемных подшипников после ремонта необходимо обеспечить натяг до 0,05 мм, что достигается установкой прокладок между корпусом и крышкой.
Изношенные подшипники качения заменяют новыми и сдают для реставрации на специальные заводы (реставрированные имеют букву Р). Демонтируют подшипники с помощью съемников или пресса. При их отсутствии подшипник демонтируют легкими равномерными ударами молотка по точкам туго напрессованного кольца, расположенным диаметрально противоположно (крест-накрест), через медную или деревянную прокладку или выколотку. Подшипник следует снимать равномерно без перекоса. Для облегчения демонтажа подшипника с вала подшипник поливают горячим минеральным маслом.
Перед установкой новый подшипник промывают бензином с добавлением 6-8% минерального масла или в горячем масле (Индустриальное-12 или 20), вручную проверяют легкость его вращения укладывают на бумагу и сушат.
Подшипник напрессовывают на вал в холодном или горячем состоянии. В последнем случае, например при монтаже подшипников на валы сепараторов, подшипник нагревают в масле до 70-80 °С. Во избежание воспламенения масла, его нагревают на водяной бане или на плитке с закрытой спиралью.
При монтаже подшипника следят, чтобы торцы колец с клеймением (номером подшипника) были обращены наружу, так как уточнение номера может потребоваться при замене подшипника.
Монтируют подшипники, ударяя молотком по оправке или выколотке, изготовленным из дерева или мягкого металла (медь, алюминий), а также с помощью пресса. При посадке подшипника ударять молотком непосредственно по кольцам, сепаратору, шарикам или роликам запрещается. При этом подшипник должен плотно прилегать к заплечику вала (щуп 0,03мм не проходит).
Правильно установленный подшипник при вращении вручную должен издавать легкий равномерный шум и не должен заедать.
Ответ: Сборка узлов с подшипниками качения
Требования: подшипники качения должны легко вращаться, иметь радиальное и осевое биение в заданных пределах и занимать точное положение относительно основных баз корпуса.
Подшипник качения должен точно фиксировать положение вала в сборочной единице; на него не должны влиять дополнительные нагрузки от температурных деформаций вала и перетяжки узла при его монтаже.
Выполнение этих требований зависит от правильности выбора посадки подшипников на вал и в корпус, от точности обработки посадочных мест валов и корпусов. Выбор посадок и требований к посадочным поверхностям является задачей конструктора.
Легкое вращение и долговечность подшипников зависят от зазоров между телами качения, внутренним и наружным кольцами.
Радиальные зазоры бывают начальными, посадочными и рабочими.
При установке подшипника на вал или в корпус изменяются диаметры внутреннего и наружного колец подшипника, а следовательно, и радиальный зазор.
В процессе работы происходит нагрев колец подшипника и радиальный зазор также изменяется.
Поэтому при сборке важно обеспечить максимальное приближение посадочного радиального зазора к его расчетному значению.
Так как в процессе работы подшипника вращающееся кольцо имеет равномерный износ, то его устанавливают на вал или в корпус с гарантированным натягом.
Невращающееся кольцо при такой посадке будет иметь неравномерный износ по окружности, поэтому для него выбирают переходную посадку, обеспечивающую возможность его проворота в процессе работы.
Посадка внутренних колец подшипников качения на вал осуществляется по системе отверстия, а наружного кольца в корпус - по системе вала.
Сборка подшипниковых узлов состоит из следующих этапов: расконсервация подшипников, их контроль, установка подшипников на вал или в корпус, установка вала в корпус.
Расконсервацию подшипников проводят в 6 %-ном растворе масла, бензине или в горячих (75-85° С) антикоррозийных растворах, например, следующего состава, %: триэтаноламин 0,5-1,0, нитрат натрия 0,15-0,2, смачиватель 0,02 ... 0,1, остальное - вода.
Промывку подшипников в бензине осуществляют в специальной таре, добавляя 6...8% (по объему) минерального масла (Индустриаль-ное-12 или Минеральное-20).
Подшипники опускают в раствор и, придерживая внутреннее кольцо, вращают наружное до тех пор, пока со всех деталей не будет удалена антикоррозионная смазка.
Подшипники на вал или в корпус для сборочных единиц нормальной точности устанавливают прессованием по посадке с натягом. Более точный радиальный зазор в подшипнике обеспечивает сборка с нагревом подшипника и охлаждением вала.
При установке на вал подшипники независимо от применяемой посадки следует нагреть в минеральном масле, температура которого не должна превышать 100°С.Подшипник нагревают в масляной ванне при 80-120 °С в течение 15-20 мин. Вал охлаждают в жидком азоте до -190° С.
Кроме того, на подшипниках, поступивших на сборку, не должно быть следов коррозии, заусенцев, царапин, забоин и острых кромок; вращаться они должны плавно, без заедания. К установке подшипников приступают только после проверки посадочных мест на валу и в корпусе. Геометрические размеры и форма посадочных мест должны точно соответствовать указанным в чертеже.
В процессе запрессовки подшипника на вал или в корпус необходимо использовать специальные приспособления, имеющие направляющие и ориентирующие элементы (оправки с буртиками).
Запрессовку крупногабаритных подшипников качения выполняют с помощью специального приспособления с гидравлическим приводом.
При использовании приспособления в зону контакта сопрягаемых деталей подается масло, которое обеспечивает жидкостное или полужидкостное трение, что значительно снижает требуемое усилие запрессовки.
Часто внутреннее кольцо подшипника фиксируют на валу только за счет соответствующей посадки (рис.а), но такая фиксация не гарантирует отсутствия осевого перемещения подшипника в процессе работы.
Для надежной фиксации внутреннего кольца подшипника на валу от осевых перемещений применяют дополнительное крепление:
пружинным стопорным кольцом (рис. б), которое закладывают в кольцевую канавку на валу; торцевой шайбой (рис. в), закрепляемой на валу винтом; упорной гайкой со стопорной шайбой (рис.г); распорной втулкой с гайкой (рис. д).
Подшипники малых размеров в прецизионных изделиях целесообразно устанавливать на вал или в корпус методом ультразвуковой запрессовки, так как нагрев подшипника или охлаждение вала не обеспечивают необходимого изменения диаметра для создания монтажного зазора.
При сборке прецизионных подшипниковых опор, например в станкостроении, с целью повышения их жесткости и уменьшения осевого и радиального биений в них создают предварительный натяг. Его создают приложением постоянной осевой нагрузки, под воздействием которой происходит смещение одного из колец подшипника относительно другого на величину, равную заданному предварительному натягу.
Это смещение обеспечивает ликвидацию осевого зазора и создает начальную упругую деформацию в местах контакта рабочих поверхностей колец подшипника с телами качения.
Обеспечение радиального зазора.
Его определяют по осевому зазору в радиальном подшипнике. Вал с подшипниками устанавливают в приспособлении (рис. б).
Измерения производят до и после приложения силы pq. Разность показаний индикатора 1 дает значение осевого зазора С.
Радиальный зазор находят из формулы
где r - радиус желоба, мм; dш - диаметр шарика, мм.
Радиальный зазор в коническом роликовом подшипнике регулируют осевым смещением наружного кольца на величину е, которая связана с радиальным зазором соотношением
где - угол наклона ролика, град.
Практически осевое смещение, рассчитанное по необходимому радиальному, определяют следующим способом. Крышку 2 (рис. б) затягивают до тугого вращения вала, что гарантирует выборку всех зазоров. Измеряют зазор е. Крышку снимают, подбирают и устанавливают прокладку и возвращают крышку на место.
При сборке блока подшипников необходимо обеспечить равномерное распределение радиальной и осевой нагрузок по подшипникам.
Это достигается подбором подшипников с минимальной разницей размеров В. Распорные втулки 1 и 8 также подбирают по размерам А и А1 или совместно обрабатывают.
В узлах с подшипниками качения, работающих при больших скоростях вращения, необходимо стремиться к минимальному (нулевому) радиальному зазору для уменьшения возможных осевых колебаний
При установке вала в разъемный корпус из-за погрешностей формы гнезд под подшипник в корпусе или крышке возникает необходимость их пригонки. Ее производят пришабриванием по пятну контакта с подшипником.
Для получения пятна контакта подшипник смазывают краской, устанавливают вал в корпус и накрывают крышкой без затяжки крепежных деталей. Пришабривание позволяет получить более полное прилегание подшипника и равномерную деформацию кольца подшипника в радиальном направлении в процессе затяжки крепежных деталей.
В конструкциях, которые предусматривают регулировку осевого смещения резьбовыми деталями, зазор в подшипниках создают затяжкой резьбовой детали с силой, обеспечивающей выборку осевых зазоров.
В упорных подшипниках необходимо обеспечить нулевой осевой зазор между шариками и кольцами подшипника.
Регулировку зазора производят шайбой 2 и затяжкой болта.
Сила затяжки резьбовой детали должна иметь небольшую погрешность относительно расчетного значения. Малое радиальное смещение колец подшипника одно относительно другого гарантируют точностью обработки деталей, входящих в узел.
24. Проектирование операций сборки игольчатых подшипников.
Ответ: Монтаж игольчатых подшипников.
Применяют когда в узлах действуют большие инерционные силы, а габаритные размеры узла и его масса ограничены.
Такие подшипники имеют две рабочие поверхности - внутреннюю и наружную. В комплект входят также иглы - ролики малого диаметра и большой длины, и боковые ограничители, предупреждающие выпадание роликов из узла.
По сравнению с шариковыми и роликовыми игольчатые подшипники имеют гораздо больший радиальный зазор, соизмеримый с радиальным зазором подшипников скольжения.
Сборку с игольчатыми подшипниками начинают с подбора тел качения по размеру наружного диаметра и длине.
Точность подбора не более 0,005 мм по диаметру и 0,1 мм по длине.
Монтаж игольчатого подшипника ведется по схеме показанной на рисунке:
1. на поверхность шейки вала наносят слой консистентной смазки;
2. устанавливают вал 1 в монтажное полукольцо 2;
3. в зазор между валом 1 и монтажным полукольцом 2 вводят, постепенно поворачивая вал, последовательно игольчатые ролики 3 до тех пор, пока весь комплект игл не будет установлен;
4. надевают на вал охватывающую деталь, смещая монтажное кольцо.